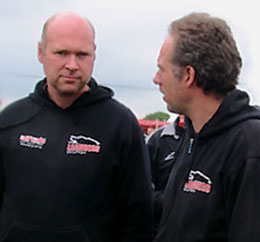
The Leanders brothers, Ulf and Jörgen, are well known faces in the European drag racing community. Both started their drag racing careers as drivers in the early 1990s, each having a Plymouth. After that they bought a Dodge Dart which they took turns in driving from ‘96 to ‘98 in the Nordic Pro Street Cup. When they first entered the Top Methanol Funny Car class in 1999 the idea was to continue taking turns to drive, Ulf the first season and Jörgen the next, but after half of the first season Jörgen told Ulf that he wanted his younger brother to continue behind the wheel of the Funny Car.
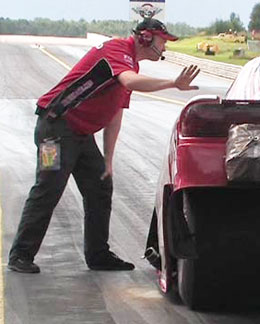
In 2005 the Leanders Bros had gone as far as they could with the clutch that was in the car. It wouldn’t do what they wanted and they were not happy with it. They ordered what was supposed to be the best clutch on the market for their methanol car from another US supplier. Both were surprised and astonished to find that the brand new clutch was an identical copy of their old one, just with a different brand name printed in the instructions folder that came with it. The new clutch had all the same problems as the old one and nothing new to offer. That was just in time for the first race of the 2005 season at Santa Pod. Although they could see by eye and by measuring that the flywheel was not straight, they had no alternative other than to put the clutch in the car. Not surprisingly they had great difficulties in getting the car down the track, and as a result damaged the flywheel.
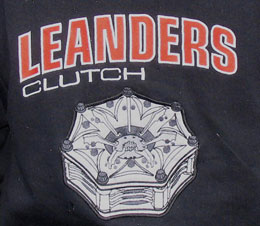
It was their dissatisfaction with what was on the market that made Ulf and Jörgen decide to develop their own clutch. Coincidently they had Ironcad as a sponsor and made good use of the Ironcad CAD programs on their computers. Neither of the brothers had much knowledge in CAD design, but they taught themselves over time. Even so, the design process was more complicated than they expected. The brothers also had a small CNC milling machine in their workshop at home but had to learn how to operate that too. Ulf says: “we have learnt by trial and error really, all through this process. We did not have much knowledge to start with and have developed everything ourselves”.
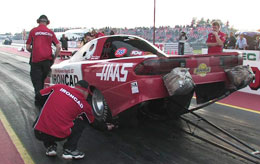
As experienced racers and mechanics they knew what they wanted to improve on in their clutch design, compared to existing clutches on the market. For instance they wanted to prevent tear to the rear main bearing, which had been a problem with previous clutches. “There can be all kinds of problems if the clutch tears too much”, says Ulf. “When that happens the angle of the arms becomes different”. Being new to the design process gave them an advantage, as they didn’t feel they had to start with a design similar to existing clutches. “There was no point in copying or using parts of designs that we did not think worked. It would maybe have meant we could get our clutch to work as well or more reliably than existing clutches on the market, but we wanted something superior to that”.
It is not an understatement to say the Leanders Bros are in control of the production of their clutches, as 90% of a Leanders Clutch is produced in their own workshop situated in Grängsbo a few hours drive north of Stockholm, Sweden. The first Leanders clutch prototype was ready for testing in their own methanol funny car late during the 2006 racing season. It took two versions and two seasons of testing until they felt ready to market and sell the Leanders Clutch to other teams in 2008. What they had at that time was an 11” clutch suited for methanol cars like Funny Cars and Pro Mods.
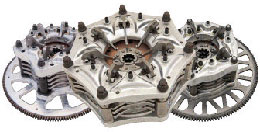
The introduction of Leanders Clutch was made in the US at the PRI (Performance Racing Industry) show in December 2008. Ulf and Jörgen made sure to submit their clutch to the SFI testing and certification process, which means it is legal to use in the US, Europe and Australia.
The major advantage with a Leanders clutch, says Ulf, is that it is very solid and stable, non- flexing so to speak. A big help in learning and getting the result they was looking for, was the development and construction of a clutch dyno system in 2007. They contacted the computer expert Johan Hartwig, to build them a computer that would fit inside the dyno, placed at the centre of the axle where the centrifugal forces don’t affect the measurements.
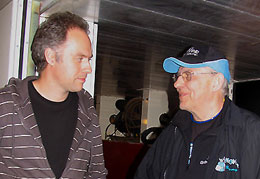
Ulf says that a methanol clutch produce 10,000 pounds of pressure. Adding a mere 60 grams of weight on the arms mean the pressure on the doughnut increases by approximately 3.9 tonnes! Under circumstances like that it is crucial that the arms have the right design and are made of the right material.